robutacion
Member
Hi everyone,
I have just finished putting this information on this thread, when I realize that for all purposes and reasons, this information should be on its own for better acknowledgment and reach by everyone, sorry -D- NC!.
So, here we go...!
Thank you for posting that, I wasn't aware that Liquid Glass could appear as a totally different product as the one I have. The Liquid Gloss I always known and order is a 2 part water based epoxy (in the old days wasn't water based but acetone or thiner based, nasty stuff for the health...!). The consistency of this gloss coat is like a "runny" honey on both parts A & B, both totally clear before and after mixed, particularly made to be poured
into flat surfaces so that the product can level itself before cure. This can make things a little difficult and tricky if the area you want to apply the coat on is not flat, this can be overcome by rotating the piece slowly continuously until the curing/drying starts, normally about 30 minutes.
This stuff is recommended as a single coat only, the consistency is similar to 50 coats with a normal varnish and thickness about 1mm or more if you want. You can control this by the quantity you pour into the surface to coat, particularly is is flat. On a pen, the material used for the pen has to be taken down to a under size of at least 0.5mm, then you control the thickness you want on it by doing the following;
*- If you want a minimal (about 0.5mm) coat, you don't wait for the mix to start setting (start thickening) about 15 minutes or so, after you have your bushings covered (tape or something- clear sticky tape is good and thin), there is if you coat it while the barrels are on the mandrel, but I would recommend doing it with the barrels inserted in a wooden/metal/alluninium rod with a "nudge" fit to the tubes so that they turn when mounted on the lathe (in between centers), you use the mix while it is most soft, there is immediately after mixing, using a small brush you control the amount of material you are putting on (do it with the lathe OFF).
Brush the barrel lengthwise as if you were "painting" it, when the surface of the barrel(s) is/are all covered then, turn the lathe on the slowest speed you have, let it turn for 30 minutes or so, make sure there is no dust floating around while the coating is raw (not cured/dry).
With this method you can do a reasonable number of barrels in one go, depending on the lathe bed length and stiffness of the rod you use, obviously!
Regardless of how rough the coating looks when you are brushing it, as soon as the lathe starts turning, the coating will totally level itself out, leaving this
"glass" finish, reason to the product's name. The durability is identical to the products used to varnish wood/cork floors. It can also be use for casting ( more expensive than traditional castings resins), mainly if a pure water crystal clear finish is required.
After the coat is dry, (about 12 hours) you can proceed with the normal steps as you would do if the barrels have been coated with any other product, and then put all the bits together and admire the gloss finish achieve without any polish. Remember drying time and curing time are 2 very different things, care has to be taken when assembling the pen inside of the first 24 hours, the fully cure is achieved in temps, about 20C within 2 weeks, take this into consideration when you require to put your pens into transport and hands traffic, etc.
OK, I'm done...!
Sorry is it took this long but, it did become apparent to me that my reference to the Liquid Glass, has brought some confusing and concerns due to the name existing under a totally different product(s).
The product is also known as water based Liquid Gloss Epoxy!
http://www.amcsupplies.com.au/catalo...loss-125ml.gif
This pic below is a recent sample of the product but without being on the lathe to turn and spread evenly (leveling), I started mixing the product without realizing that I had 12 samples to do and only one lathe with a chuck on (the other GMC lathe is working as a disc sander!) so, I simply brushed the product on each blank (sample), hang it by the hook, do another and turn the first one upside-down, do the next, and the next and the next...! I was running for a little while, then when all coated, I keep rotating them manually until my hands couldn't do it no more...! don't worry, I've learn my lesson..., don't start mixing stuff that is going to start drying within minutes, without making sure you're ready...!
Cheers
George
I have just finished putting this information on this thread, when I realize that for all purposes and reasons, this information should be on its own for better acknowledgment and reach by everyone, sorry -D- NC!.
So, here we go...!
Thank you for posting that, I wasn't aware that Liquid Glass could appear as a totally different product as the one I have. The Liquid Gloss I always known and order is a 2 part water based epoxy (in the old days wasn't water based but acetone or thiner based, nasty stuff for the health...!). The consistency of this gloss coat is like a "runny" honey on both parts A & B, both totally clear before and after mixed, particularly made to be poured
into flat surfaces so that the product can level itself before cure. This can make things a little difficult and tricky if the area you want to apply the coat on is not flat, this can be overcome by rotating the piece slowly continuously until the curing/drying starts, normally about 30 minutes.
This stuff is recommended as a single coat only, the consistency is similar to 50 coats with a normal varnish and thickness about 1mm or more if you want. You can control this by the quantity you pour into the surface to coat, particularly is is flat. On a pen, the material used for the pen has to be taken down to a under size of at least 0.5mm, then you control the thickness you want on it by doing the following;
*- If you want a minimal (about 0.5mm) coat, you don't wait for the mix to start setting (start thickening) about 15 minutes or so, after you have your bushings covered (tape or something- clear sticky tape is good and thin), there is if you coat it while the barrels are on the mandrel, but I would recommend doing it with the barrels inserted in a wooden/metal/alluninium rod with a "nudge" fit to the tubes so that they turn when mounted on the lathe (in between centers), you use the mix while it is most soft, there is immediately after mixing, using a small brush you control the amount of material you are putting on (do it with the lathe OFF).
Brush the barrel lengthwise as if you were "painting" it, when the surface of the barrel(s) is/are all covered then, turn the lathe on the slowest speed you have, let it turn for 30 minutes or so, make sure there is no dust floating around while the coating is raw (not cured/dry).
With this method you can do a reasonable number of barrels in one go, depending on the lathe bed length and stiffness of the rod you use, obviously!
Regardless of how rough the coating looks when you are brushing it, as soon as the lathe starts turning, the coating will totally level itself out, leaving this
"glass" finish, reason to the product's name. The durability is identical to the products used to varnish wood/cork floors. It can also be use for casting ( more expensive than traditional castings resins), mainly if a pure water crystal clear finish is required.
After the coat is dry, (about 12 hours) you can proceed with the normal steps as you would do if the barrels have been coated with any other product, and then put all the bits together and admire the gloss finish achieve without any polish. Remember drying time and curing time are 2 very different things, care has to be taken when assembling the pen inside of the first 24 hours, the fully cure is achieved in temps, about 20C within 2 weeks, take this into consideration when you require to put your pens into transport and hands traffic, etc.
OK, I'm done...!
Sorry is it took this long but, it did become apparent to me that my reference to the Liquid Glass, has brought some confusing and concerns due to the name existing under a totally different product(s).
The product is also known as water based Liquid Gloss Epoxy!
http://www.amcsupplies.com.au/catalo...loss-125ml.gif
This pic below is a recent sample of the product but without being on the lathe to turn and spread evenly (leveling), I started mixing the product without realizing that I had 12 samples to do and only one lathe with a chuck on (the other GMC lathe is working as a disc sander!) so, I simply brushed the product on each blank (sample), hang it by the hook, do another and turn the first one upside-down, do the next, and the next and the next...! I was running for a little while, then when all coated, I keep rotating them manually until my hands couldn't do it no more...! don't worry, I've learn my lesson..., don't start mixing stuff that is going to start drying within minutes, without making sure you're ready...!
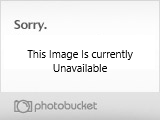
Cheers
George