robutacion
Member
Hi peoples,
Everyone knows that, wood hardness is something that we, woodworkers, turners, etc., deal with on a daily basis, sometimes its turns out to be a lot more than just, "wood is a bit soft...!", how soft is it...??? its softness is a lot more important than its hardness, in most cases, particularly for pen turners where, attempting to handle a blank with soft patches or a blank that is all very soft, without any sort of hardening or preparation, can turn into a nightmare and more often that not, a fail...!
In our days, where home wood stabilization is no longer a problem, I wonder what people use to determine if the blank is too soft to attempt to turn, totally raw. Sure, thin CA saturation can be as effective as stabilization, probably a little more expensive, a little less effective in bigger wood dimensions and certainly, a lot more dangerous to ones health (fumes).
Does one need a specific "Durometer" (hardness gauge)...??? sure not, particularly when until recently, those instruments were extremely expensive...???
Have you have asked a "gadgets" person, if he or she wouldn't consider every possibility to own them, even if they are never used or used a couple of times...??? well, I can tell you what the response/answer would be, as I'm one of those...!:wink:
If there is something that I really like about todays technology, is the fact that, made in China or thereabouts, allows you to own gadgets that you never thought possible, a decade or two, ago.:wink::biggrin:
With this in mind, I come across an instrument on eBay that got my attention, first for what it was made to do and secondly, the very affordable price of under $50.00 shipped, such as this one (this was not from where I order mine but is the same thing and has more details about the items than the sire I got it from, a little cheaper too...!)
There are 3 types, A, C and D, I didn't realise that until I got mine and searched a little more, as I didn't like the tip and the softness of the spring. I then found out that, I should have got the "D" type, as shown below.
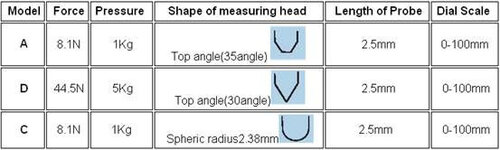
I decided to pull it appart and make a few modifications, one was to sharpen the probe end into a point and second was to, replace the spring with a much stronger one.
I have never used these gauges before but, I'm certain that I made it very similar to the "D" type and therefore a lot more suitable for the intended purpose...!
The final adjustment was made on the screw at the top of the instrument and under the top "T" knob, screwing it in or out, I manage to get the low readings on the soft wood as I wanted and at the same time, have better readings on the harder woods. I doubt that the "official calibration" of the instrument is off however, I don't know that for sure and it doesn't really matter to me...!
OK so, with the gauge reading the way I wanted, I started to do some testings and see what would happen/say. Next are some pics of the instrument after modified and a test that I done to confirm if I could still read the 100% the unit was made for, I used the metal bandsaw table and the results are very close, at 94% so that is the hardest it will read, on totally solid steel, wood has to read lower than that...!
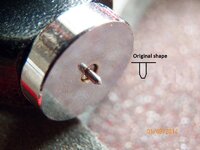
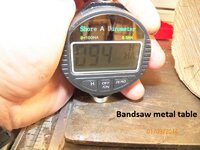
After I got the maximum reading calibrated, I decided to make some readings on materials that we all recognize as soft, and everything in between. My benchmark was to see what the readings would be with some true Cork (bark), not the softest but surely one that we are all familiar with...!
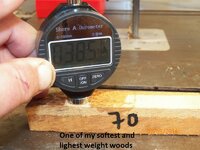
I have only one other wood/plant type material, that is softer than the Coral tree, View attachment 121570 View attachment 121571 and that is the "Century Plant", that I cut from this area a few years ago, not the one is the pic below (I got this on Google) but mine was a lot bigger, I got 7 pieces of my height (approx 170cm/67") that made it about 12 meters tall...!
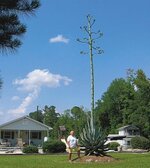
This material has the same consistency and weight to the Polystyrene even though at the time, and before I got my stabilization gear, I made pen blanks and pens out of it however, I done a lot more work with this material, after I started stabilizing...!
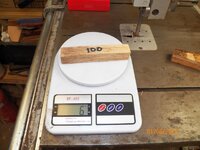
My hardest wood, is the #66 Australian Swamp Mallet Gum, that I have growing in the area, as the name indicates, this is a tough wood when properly dried.
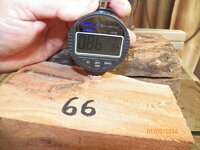
Next, is a series of pics of different of my woods tested for hardness and compared with its weight, against the hardest and heaviest woods and to the softest and lightest woods. My apologies if the digital numbers are a little difficult to read on some samples, was the position I had to put the camera to avoid the flash blindness/witness that caused it, the instrument shown the digits very clearly and vividly...!
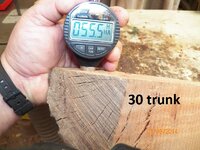
View attachment 121590 View attachment 121591
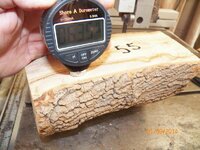
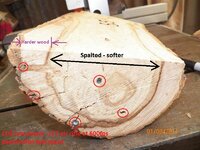
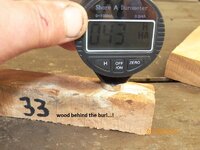
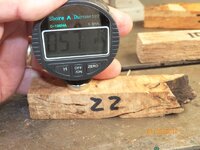
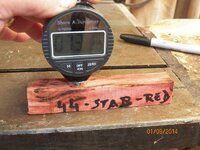
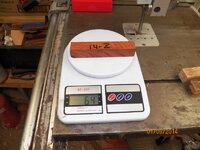
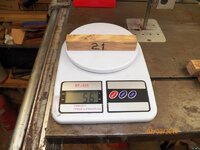
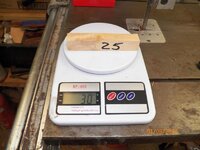
Often, the question is asked, how hard does a wood become after stabilized...???
I decided to show you this example of something that is not really wood, is 100% buoyant like cork, is not the best soaking materials, (by the contrary) however, it shows a considerable/significant hardness difference between raw and stabilized, and this is the Pine bark...!
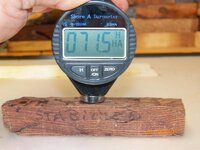
One other common question is also, why do I have so much trouble with blanks that are made with a combination of wood(other) and resin (polyester but not only), they keep exploding on me..???
Well, one of the biggest culprits is, the hardness difference in between the materials used in that blank. Even when these blanks are made with wood and resin, various things should be considered, not all woods have the same hardness and not all acrylics/resins have the same hardness, also.
So, why do they blow appart...??? simply look at the 2 pics below, the wood used in that Resifill (cast) blank is my #22 Olive root, a very medium to soft wood, compared with the readings you see on the resin patch on that same blank so, and unless your tools are very sharp, you have the right cutting techniques or use the flap disc, any minimal catch from the transaction of the softer to the hardest material, will result in a bad chip, some separation or the blanks disintegrates in front of you and that, is not the blanks fault...!
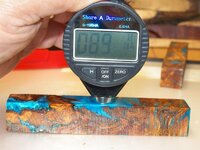
And to wrap up this hardness tests thread, I will leave you with 2 interesting pics of the "famous" #45 Banksia Hairy pods Resifills pen blanks, where I tested the hardness of the Banksia Hairy pod "eye", that has been stabilized and then cast, the blanks was sanded so there is no resin over that part of the pod, it is solid from the stabilization and shows no hardness difference, from what the blanks has at the middle point where, the hairs joint from the 2 pod halves, there is mostly resin (polyester)...!
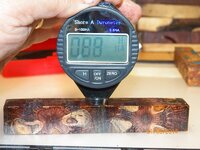
What am I trying to say...???
Well, make your own judgment...!:wink::biggrin:
Cheers
George
Everyone knows that, wood hardness is something that we, woodworkers, turners, etc., deal with on a daily basis, sometimes its turns out to be a lot more than just, "wood is a bit soft...!", how soft is it...??? its softness is a lot more important than its hardness, in most cases, particularly for pen turners where, attempting to handle a blank with soft patches or a blank that is all very soft, without any sort of hardening or preparation, can turn into a nightmare and more often that not, a fail...!
In our days, where home wood stabilization is no longer a problem, I wonder what people use to determine if the blank is too soft to attempt to turn, totally raw. Sure, thin CA saturation can be as effective as stabilization, probably a little more expensive, a little less effective in bigger wood dimensions and certainly, a lot more dangerous to ones health (fumes).
Does one need a specific "Durometer" (hardness gauge)...??? sure not, particularly when until recently, those instruments were extremely expensive...???
Have you have asked a "gadgets" person, if he or she wouldn't consider every possibility to own them, even if they are never used or used a couple of times...??? well, I can tell you what the response/answer would be, as I'm one of those...!:wink:
If there is something that I really like about todays technology, is the fact that, made in China or thereabouts, allows you to own gadgets that you never thought possible, a decade or two, ago.:wink::biggrin:
With this in mind, I come across an instrument on eBay that got my attention, first for what it was made to do and secondly, the very affordable price of under $50.00 shipped, such as this one (this was not from where I order mine but is the same thing and has more details about the items than the sire I got it from, a little cheaper too...!)
There are 3 types, A, C and D, I didn't realise that until I got mine and searched a little more, as I didn't like the tip and the softness of the spring. I then found out that, I should have got the "D" type, as shown below.
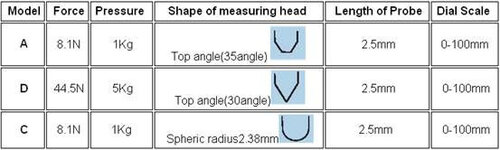
I decided to pull it appart and make a few modifications, one was to sharpen the probe end into a point and second was to, replace the spring with a much stronger one.
I have never used these gauges before but, I'm certain that I made it very similar to the "D" type and therefore a lot more suitable for the intended purpose...!
The final adjustment was made on the screw at the top of the instrument and under the top "T" knob, screwing it in or out, I manage to get the low readings on the soft wood as I wanted and at the same time, have better readings on the harder woods. I doubt that the "official calibration" of the instrument is off however, I don't know that for sure and it doesn't really matter to me...!
OK so, with the gauge reading the way I wanted, I started to do some testings and see what would happen/say. Next are some pics of the instrument after modified and a test that I done to confirm if I could still read the 100% the unit was made for, I used the metal bandsaw table and the results are very close, at 94% so that is the hardest it will read, on totally solid steel, wood has to read lower than that...!

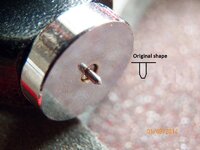
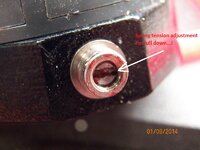
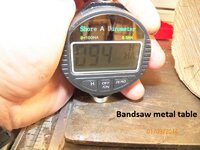
After I got the maximum reading calibrated, I decided to make some readings on materials that we all recognize as soft, and everything in between. My benchmark was to see what the readings would be with some true Cork (bark), not the softest but surely one that we are all familiar with...!
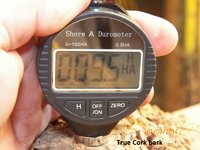
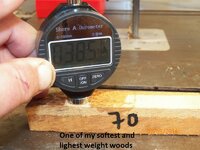
I have only one other wood/plant type material, that is softer than the Coral tree, View attachment 121570 View attachment 121571 and that is the "Century Plant", that I cut from this area a few years ago, not the one is the pic below (I got this on Google) but mine was a lot bigger, I got 7 pieces of my height (approx 170cm/67") that made it about 12 meters tall...!
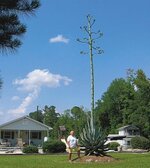
This material has the same consistency and weight to the Polystyrene even though at the time, and before I got my stabilization gear, I made pen blanks and pens out of it however, I done a lot more work with this material, after I started stabilizing...!
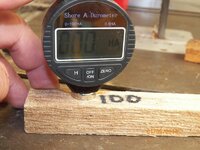
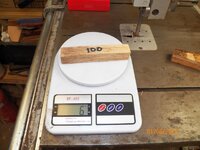
My hardest wood, is the #66 Australian Swamp Mallet Gum, that I have growing in the area, as the name indicates, this is a tough wood when properly dried.
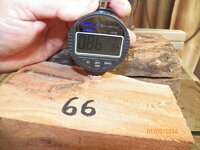
Next, is a series of pics of different of my woods tested for hardness and compared with its weight, against the hardest and heaviest woods and to the softest and lightest woods. My apologies if the digital numbers are a little difficult to read on some samples, was the position I had to put the camera to avoid the flash blindness/witness that caused it, the instrument shown the digits very clearly and vividly...!
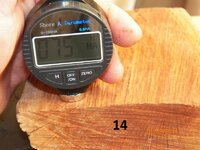
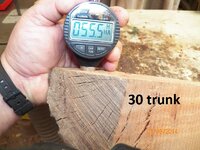
View attachment 121590 View attachment 121591
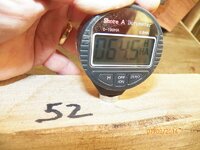
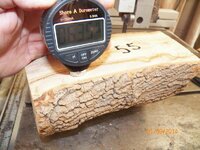
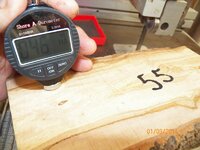
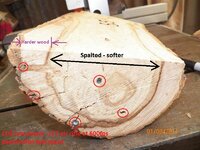
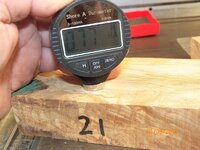
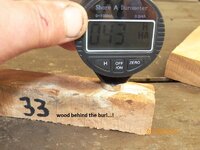
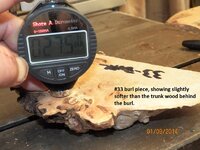
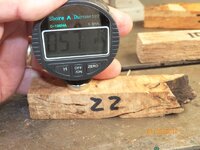
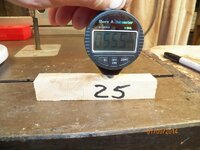
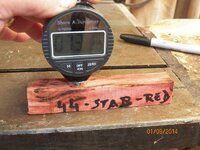
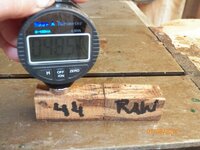
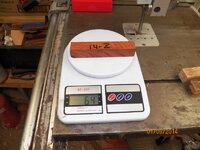
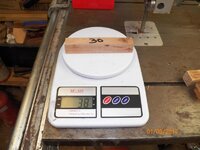
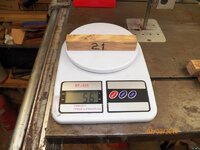
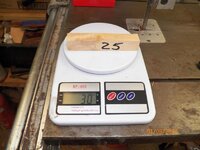
Often, the question is asked, how hard does a wood become after stabilized...???
I decided to show you this example of something that is not really wood, is 100% buoyant like cork, is not the best soaking materials, (by the contrary) however, it shows a considerable/significant hardness difference between raw and stabilized, and this is the Pine bark...!
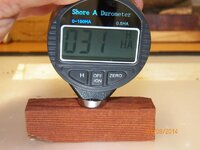
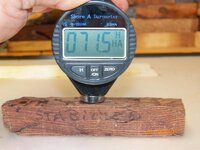
One other common question is also, why do I have so much trouble with blanks that are made with a combination of wood(other) and resin (polyester but not only), they keep exploding on me..???
Well, one of the biggest culprits is, the hardness difference in between the materials used in that blank. Even when these blanks are made with wood and resin, various things should be considered, not all woods have the same hardness and not all acrylics/resins have the same hardness, also.
So, why do they blow appart...??? simply look at the 2 pics below, the wood used in that Resifill (cast) blank is my #22 Olive root, a very medium to soft wood, compared with the readings you see on the resin patch on that same blank so, and unless your tools are very sharp, you have the right cutting techniques or use the flap disc, any minimal catch from the transaction of the softer to the hardest material, will result in a bad chip, some separation or the blanks disintegrates in front of you and that, is not the blanks fault...!
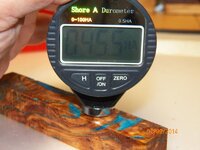
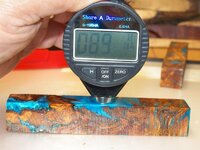
And to wrap up this hardness tests thread, I will leave you with 2 interesting pics of the "famous" #45 Banksia Hairy pods Resifills pen blanks, where I tested the hardness of the Banksia Hairy pod "eye", that has been stabilized and then cast, the blanks was sanded so there is no resin over that part of the pod, it is solid from the stabilization and shows no hardness difference, from what the blanks has at the middle point where, the hairs joint from the 2 pod halves, there is mostly resin (polyester)...!
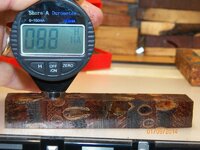
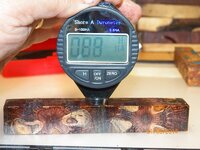
What am I trying to say...???
Well, make your own judgment...!:wink::biggrin:
Cheers
George
Last edited: