airborne_r6
Member
- Joined
- Oct 28, 2008
- Messages
- 279
I wanted to make a blank squaring jig to use on my 12" disc sander but was not happy with any of the existing jigs out there. The main reasons included:
-only one size of rod holding the blank
-not adjustable for square, necessitating a high degree of accuracy in manufacture
With those problems in mind I set out to design a jig that would hold the transfer rods we all use to knock apart pens in such a way that they could be easily swapped out so that the blank is always on the best size of rod without needing to use any sleeves. I always wanted a way to be able to adjust the jig to square with the disc so that it is always accurate. I also wanted it to be easy to use.
This is what I came with. I first built a prototype a couple years ago out of MDF. When that worked exactly as I had planned I rebuilt it out of 3/4 Baltic Birch plywood and took pictures of the process. That was longer ago than I am going to admit, but cut me some slack, I am in medical school.
So without further ado, I give you the best blank squaring jig ever. At least in my not so humble opinion.
The transfer punch is held securely by the captured bolt and punches a swapped out easily by simply loosening the bolt. No adjustment is necessary for different size punches.
The punch carriage adjusts easily side to side and up and down. One of the two bolts securing the carriage in each direction is slightly enlarged. Simply place a small square between the punch and the disc, loosen the appropriate nut, adjust as necessary and tighten the nut. It holds very securely.
To use the jig just slide the whole jig to the left, it's mounted to a miter bar. Once the punch is clear of the disc, place a blank on the disc and slide the jig back to the right. Then push the blank into the disc. Because the blank is held securely on the proper size of punch it takes almost no effort and can easily be done from the end of the blank away from the disc without worrying about slipping off and sticking your fingers into the sander. Multiple blanks can be sanded quickly and safely without needing to stop the sander.
Super simple, super fast and super accurate.
I am working on making a tutorial that will hopefully go in the library with a materials list, directions and a complete plan.
-only one size of rod holding the blank
-not adjustable for square, necessitating a high degree of accuracy in manufacture
With those problems in mind I set out to design a jig that would hold the transfer rods we all use to knock apart pens in such a way that they could be easily swapped out so that the blank is always on the best size of rod without needing to use any sleeves. I always wanted a way to be able to adjust the jig to square with the disc so that it is always accurate. I also wanted it to be easy to use.
This is what I came with. I first built a prototype a couple years ago out of MDF. When that worked exactly as I had planned I rebuilt it out of 3/4 Baltic Birch plywood and took pictures of the process. That was longer ago than I am going to admit, but cut me some slack, I am in medical school.
So without further ado, I give you the best blank squaring jig ever. At least in my not so humble opinion.
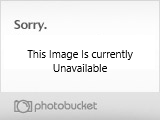
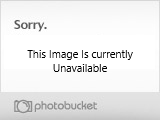
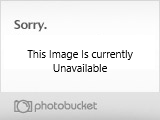
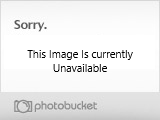
The transfer punch is held securely by the captured bolt and punches a swapped out easily by simply loosening the bolt. No adjustment is necessary for different size punches.
The punch carriage adjusts easily side to side and up and down. One of the two bolts securing the carriage in each direction is slightly enlarged. Simply place a small square between the punch and the disc, loosen the appropriate nut, adjust as necessary and tighten the nut. It holds very securely.
To use the jig just slide the whole jig to the left, it's mounted to a miter bar. Once the punch is clear of the disc, place a blank on the disc and slide the jig back to the right. Then push the blank into the disc. Because the blank is held securely on the proper size of punch it takes almost no effort and can easily be done from the end of the blank away from the disc without worrying about slipping off and sticking your fingers into the sander. Multiple blanks can be sanded quickly and safely without needing to stop the sander.
Super simple, super fast and super accurate.
I am working on making a tutorial that will hopefully go in the library with a materials list, directions and a complete plan.