W.Y.
Member
This is the first in a series of captive ring goblets I will be making (as well as a few with no rings) for Christmas craft sales .
I was right out of goblets again and they sell real good especially if they are made with wood with nice markings.
I was right out of goblets again and they sell real good especially if they are made with wood with nice markings.
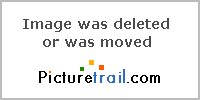