mark james
IAP Collection, Curator
Introducing, "The Dud." I fully expected this to explode at numerous times during turning. But thankfully, the bomb squad outfit was not necessary (as typical, I did wear a full face shield).
Two different Trustone blanks, aluminum sheeting, 2 part epoxy, cutting fluid for the drill, HSS roughing gouge/spindle gouge, Magic Skew Round Bit, wet sanded with Abranet then Micromesh, McGuires polish, Renaissance Wax, my lucky rabbit's foot.
As explained in a different thread, after constructing the blank, I was very concerned about drilling through the aluminum sheeting parallel with the drill bit. The technique for encasing and drilling the blank is detailed here: Roy Quast's Technique.
Not well aligned, and one end is undercut, but for a first attempt, I'm OK with it. 95% of my experience turning/segmenting is with wood, so this had the potential for a few surprises.
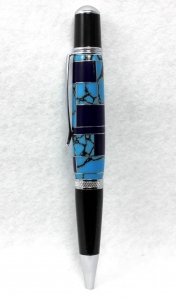
View in Gallery
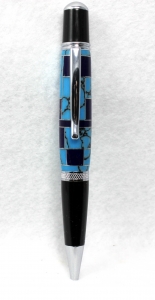
View in Gallery
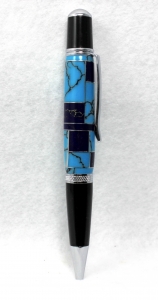
View in Gallery
Two different Trustone blanks, aluminum sheeting, 2 part epoxy, cutting fluid for the drill, HSS roughing gouge/spindle gouge, Magic Skew Round Bit, wet sanded with Abranet then Micromesh, McGuires polish, Renaissance Wax, my lucky rabbit's foot.
As explained in a different thread, after constructing the blank, I was very concerned about drilling through the aluminum sheeting parallel with the drill bit. The technique for encasing and drilling the blank is detailed here: Roy Quast's Technique.
Not well aligned, and one end is undercut, but for a first attempt, I'm OK with it. 95% of my experience turning/segmenting is with wood, so this had the potential for a few surprises.
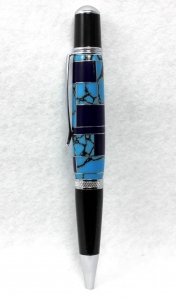
View in Gallery
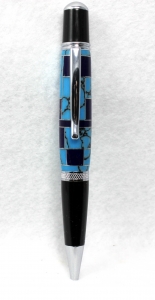
View in Gallery
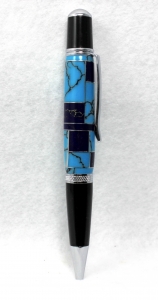
View in Gallery