Fine Engineer
Member
I'm still new at this and exploring the nearly unlimited things we can do with these small projects. In making some blanks for Christmas presents, and exploring some different metal inserts, I had some successes, and a pretty significant failure. But those are what we learn most from, right?
So first the successes. I made a couple of pens with a thin metal inlay in them. The first was kind of a mess, but the second one came out much closer to what I was trying to do.
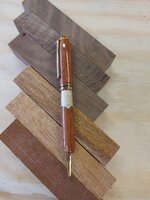
I tried making the 'V' cuts freehand on the band saw, and the intersecting bits just didn't line up well. What was needed was a jig to improve the precision. So Last weekend, I came up with this; A simple 45° fence and a rail to fit in the groove on the table. I set the end stop by using a sacrificial blank and slowly moved up the stop until the cuts from each side met cleanly in the middle. This was still a little fidgety, so I'll ultimately make something that will be drastically over engineered and complicated, but this works for now.
It's very simple, but it did do a good job of allowing me to make repeatable cuts. Here are the blanks that I put together using thsi jig;
I was able to make 6 of each of these with a high degree of precision. Pen kits are on there way, so I'll be turning these next weekend.
From my earlier project, I found that you don't even notice the thin aluminum (soda can metal) when turning. And this is what brings me to the failure.
Using the same jig, I made 4 cuts in some Mahogany to insert some .050" copper. I cut a strip and since it was a tad tight, took it to my belt sander and thinned it out just a touch. Make a cut, Add the metal, make a cut and add the metal, similar to making a Celtic Knot, but only cutting the blank half way through rather than all the way. Once it was all done and sanded square again, I cut the blank, glued in the brass tubes, and set it up on the lathe. This is where the learning comes in.
The copper cut just fine on the band saw, but was much tougher than the wood to cut on the lathe. The carbide tools handled it OK, but they kept grabbing, and eventually tore out a piece of the copper;
I was able to fill the hole, but it really blemished the finished look. What I think I need to do next time is to round the blank off more at the band saw before chucking it up on the lathe, and then be much more careful in turning down the metal section. I found that a slower speed and the square chisel rather than the round one handled the copper better. I love the look, and will try this again.
On the plus side, the jig helped the pattern come out perfectly as far as alignment goes.
So a couple of successes, and one significant failure. Not a big deal as it is only a little time and a couple dollars wasted. And not really wasted, as the pen is still usable, just a bit blemished.
For anybody else that wants to try this, I hope this helps at least a little.
Happy Holidays
Jeff
So first the successes. I made a couple of pens with a thin metal inlay in them. The first was kind of a mess, but the second one came out much closer to what I was trying to do.
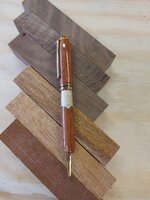
I tried making the 'V' cuts freehand on the band saw, and the intersecting bits just didn't line up well. What was needed was a jig to improve the precision. So Last weekend, I came up with this; A simple 45° fence and a rail to fit in the groove on the table. I set the end stop by using a sacrificial blank and slowly moved up the stop until the cuts from each side met cleanly in the middle. This was still a little fidgety, so I'll ultimately make something that will be drastically over engineered and complicated, but this works for now.
It's very simple, but it did do a good job of allowing me to make repeatable cuts. Here are the blanks that I put together using thsi jig;
I was able to make 6 of each of these with a high degree of precision. Pen kits are on there way, so I'll be turning these next weekend.
From my earlier project, I found that you don't even notice the thin aluminum (soda can metal) when turning. And this is what brings me to the failure.
Using the same jig, I made 4 cuts in some Mahogany to insert some .050" copper. I cut a strip and since it was a tad tight, took it to my belt sander and thinned it out just a touch. Make a cut, Add the metal, make a cut and add the metal, similar to making a Celtic Knot, but only cutting the blank half way through rather than all the way. Once it was all done and sanded square again, I cut the blank, glued in the brass tubes, and set it up on the lathe. This is where the learning comes in.
The copper cut just fine on the band saw, but was much tougher than the wood to cut on the lathe. The carbide tools handled it OK, but they kept grabbing, and eventually tore out a piece of the copper;
I was able to fill the hole, but it really blemished the finished look. What I think I need to do next time is to round the blank off more at the band saw before chucking it up on the lathe, and then be much more careful in turning down the metal section. I found that a slower speed and the square chisel rather than the round one handled the copper better. I love the look, and will try this again.
On the plus side, the jig helped the pattern come out perfectly as far as alignment goes.
So a couple of successes, and one significant failure. Not a big deal as it is only a little time and a couple dollars wasted. And not really wasted, as the pen is still usable, just a bit blemished.
For anybody else that wants to try this, I hope this helps at least a little.
Happy Holidays
Jeff