robutacion
Member
Hi peoples,
This thread was created after I saw someone posting a request for "help", due to some problems removing his casts from the mold(s). I was going to reply to it but then I realised that, one of the reasons why all my "information" is so scattered all over the place is due to the fact that, I tend to immediately reply to these type of questions/issues and go to any extends to provided as much information and images that are relevant to the issue but then, that info is lost in the system and almost impossible to remember/find when I need to bring it all out or someone else, does a search on the subject, many time I have no choice than do it all over again, and again...!
So, I created my own thread on the issue and I will next answer the question made on this thread that then took me to the thread suggested by Monty, here, and then expand a little on the mold making...!
Here it goes;
------------------------------------------------------------------------------
There are various issues in question here and if you allow me, I will explain...!
First of all, I never used Alumilite, all my experience is from using PR (polyester) resin so, I can not guarantee that all aspects of my observations will apply to Alumilite but, some I'm sure it will...!
The very fist thing I noticed is the way the mold is made, that alone is creating half if not more, of the problem. You don't need any divider made with the same white board material, the negatives of it are;
*- Use of extra board (expensive stuff), screws and time.
*- Increasing the contact surfaces to the board by 50% on each blank.
*- Reducing the mold capacity to half.
*- Increase the difficulty and time in removing the cast blanks from mold by 200%.
*- Inability to use these molds for an identical batch/block (normally 6 blanks) of only resin blanks where a double or triple colours are use and then swirled (moved around) to created the desired effects, etc....!
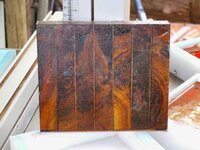
So, how do you keep the blanks separate...??? this is when you have to consider what you have/will use to cut in between the cast blanks, what I mean is, if you use a bandsaw or a table saw, the blades will have different thicknesses so, you cut strips of wood of the same thickness of the blade you will use.
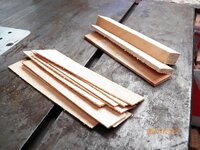
Those wood separators should also be the some hight/depth as the blanks you are casting (floating issues, explained next) so, if your blanks are 21mm square like mine, get a board of timber of that thickness about 11" long (makes 2 separators) and rip it into strips of the desired thickness, then cut to length (same as the blanks).
Simply put one of these wood separators in between each blank (you don't need it at the side the blank touches the mould), adjust the spaces with a few more strips at the last blank put in the mold, between the last blank and the mold side, packing it just firm but not too tight...!
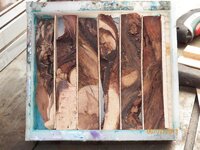
This normally stops the wood/light material to cast to float to the surface when the resin is poured or when the molds are put under pressure however, is safer to use some wood strips and some tape to wrap the blanks to the mold, stopping them to float.
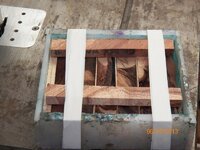
There is a simple way to get those blanks pushed down and kept there, look at the next pics,
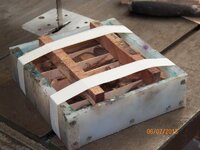
I never considered to plan/smooth the white boards surface as I didn't expect much trouble with them however, I started using PVA release agent from the very beginning. There were 2 main reasons for that, one to make easier to remove the blanks after cast but also, to seal the joints of the mold.
Before I used the molds coated each one with 4 generous coats, particularly at the board joints. I let it dry in between coats and while there is only one panel that is removed each time I want to remove the cast blanks, all other joints will soon get a good seal from the resin drying on it but, the panel that is removed each time, will need something to seal it before the resin pour, otherwise it may leak and quite badly sometimes so, I remove that possibility by coating the mold with the release agent, putting a fair amount at the removable panel and tip it upright so that the release agent penetrates the panel joints. In less than 30 minutes the release agent is dry and all that extra liquid at the panel joints, has soaked in and sealed the mold...!
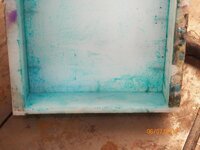
Ideally, when construction your molds out of the white boards, I suggest using at least 12mm from the bottom and the 2 longer sides, there are the panels where the screws will go in so, it needs some "meat", while the 2 side panels (end caps), I suggest using the 5 or 6mm boards.
These 2 thinner end panels will make a big difference for the mold capacity, the average pressure pots have a inner diameter that will allow about 6"1/2 square mold, for average blanks sizes @ 21mm square x 130mm long a mold with inner dimensions of 132mm long x 150mm wide, endup finished at 6" x 6"1/2.
Another thing I suggest when constructing your molds is to remember to use the smallest gauge and length possible on the end panels (thinner board), mark the panel you want to use first as the removable panel and keep using it until the screws no longer hold and you have to go to the nest gauge and length, to screw into fresh plastic.
You can continue using the same panel, but I swap over and mark the other end panel as the removable one from then on. It will be a time were the screws no longer hold and you have to do the same as the other panel and you keep swapping around in between those 2 end panels, upgrading the screws size when needed until, the holes are that big that is time to make new molds...!
The next pics I show the 3 screws sizes I've used so far, I may be able to upgrade 2 more times but these molds have cast a lot of blanks...!
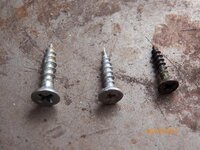
Well, I think this will cover the making and maintenance of white board made molds, if you need any further assistance, let me know...!
Cheers
George
This thread was created after I saw someone posting a request for "help", due to some problems removing his casts from the mold(s). I was going to reply to it but then I realised that, one of the reasons why all my "information" is so scattered all over the place is due to the fact that, I tend to immediately reply to these type of questions/issues and go to any extends to provided as much information and images that are relevant to the issue but then, that info is lost in the system and almost impossible to remember/find when I need to bring it all out or someone else, does a search on the subject, many time I have no choice than do it all over again, and again...!
So, I created my own thread on the issue and I will next answer the question made on this thread that then took me to the thread suggested by Monty, here, and then expand a little on the mold making...!
Here it goes;
------------------------------------------------------------------------------
There are various issues in question here and if you allow me, I will explain...!
First of all, I never used Alumilite, all my experience is from using PR (polyester) resin so, I can not guarantee that all aspects of my observations will apply to Alumilite but, some I'm sure it will...!
The very fist thing I noticed is the way the mold is made, that alone is creating half if not more, of the problem. You don't need any divider made with the same white board material, the negatives of it are;
*- Use of extra board (expensive stuff), screws and time.
*- Increasing the contact surfaces to the board by 50% on each blank.
*- Reducing the mold capacity to half.
*- Increase the difficulty and time in removing the cast blanks from mold by 200%.
*- Inability to use these molds for an identical batch/block (normally 6 blanks) of only resin blanks where a double or triple colours are use and then swirled (moved around) to created the desired effects, etc....!
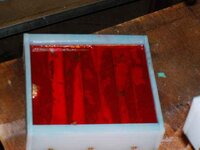
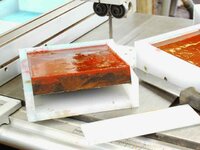
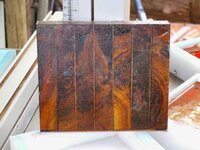
So, how do you keep the blanks separate...??? this is when you have to consider what you have/will use to cut in between the cast blanks, what I mean is, if you use a bandsaw or a table saw, the blades will have different thicknesses so, you cut strips of wood of the same thickness of the blade you will use.
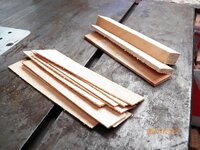
Those wood separators should also be the some hight/depth as the blanks you are casting (floating issues, explained next) so, if your blanks are 21mm square like mine, get a board of timber of that thickness about 11" long (makes 2 separators) and rip it into strips of the desired thickness, then cut to length (same as the blanks).
Simply put one of these wood separators in between each blank (you don't need it at the side the blank touches the mould), adjust the spaces with a few more strips at the last blank put in the mold, between the last blank and the mold side, packing it just firm but not too tight...!
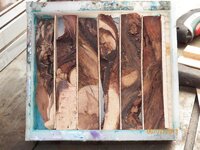
This normally stops the wood/light material to cast to float to the surface when the resin is poured or when the molds are put under pressure however, is safer to use some wood strips and some tape to wrap the blanks to the mold, stopping them to float.
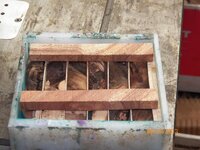
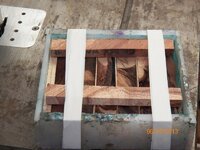
There is a simple way to get those blanks pushed down and kept there, look at the next pics,
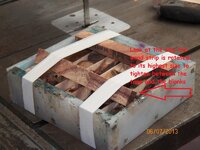
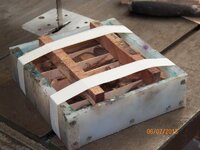
I never considered to plan/smooth the white boards surface as I didn't expect much trouble with them however, I started using PVA release agent from the very beginning. There were 2 main reasons for that, one to make easier to remove the blanks after cast but also, to seal the joints of the mold.
Before I used the molds coated each one with 4 generous coats, particularly at the board joints. I let it dry in between coats and while there is only one panel that is removed each time I want to remove the cast blanks, all other joints will soon get a good seal from the resin drying on it but, the panel that is removed each time, will need something to seal it before the resin pour, otherwise it may leak and quite badly sometimes so, I remove that possibility by coating the mold with the release agent, putting a fair amount at the removable panel and tip it upright so that the release agent penetrates the panel joints. In less than 30 minutes the release agent is dry and all that extra liquid at the panel joints, has soaked in and sealed the mold...!
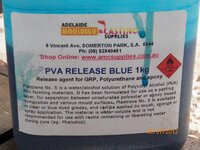
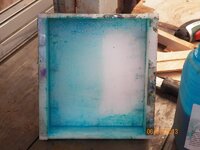
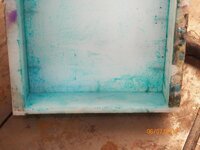
Ideally, when construction your molds out of the white boards, I suggest using at least 12mm from the bottom and the 2 longer sides, there are the panels where the screws will go in so, it needs some "meat", while the 2 side panels (end caps), I suggest using the 5 or 6mm boards.
These 2 thinner end panels will make a big difference for the mold capacity, the average pressure pots have a inner diameter that will allow about 6"1/2 square mold, for average blanks sizes @ 21mm square x 130mm long a mold with inner dimensions of 132mm long x 150mm wide, endup finished at 6" x 6"1/2.
Another thing I suggest when constructing your molds is to remember to use the smallest gauge and length possible on the end panels (thinner board), mark the panel you want to use first as the removable panel and keep using it until the screws no longer hold and you have to go to the nest gauge and length, to screw into fresh plastic.
You can continue using the same panel, but I swap over and mark the other end panel as the removable one from then on. It will be a time were the screws no longer hold and you have to do the same as the other panel and you keep swapping around in between those 2 end panels, upgrading the screws size when needed until, the holes are that big that is time to make new molds...!
The next pics I show the 3 screws sizes I've used so far, I may be able to upgrade 2 more times but these molds have cast a lot of blanks...!
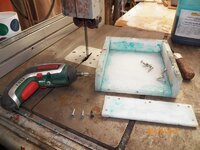
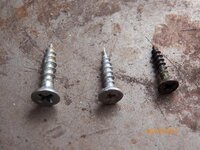
Well, I think this will cover the making and maintenance of white board made molds, if you need any further assistance, let me know...!
Cheers
George
Last edited: