NT_2112
Member
Hi all. This is a great site for a newbie like me, a big thank you to all the members.
I'm running into an issue joining a kitless pen cap and a pen body.
I made my own mandrel, as shown below. I plan to use it to hold the pen body and pen cap when I shape them on the lathe.
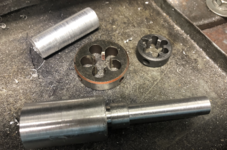
I used a M13x1 tap and die. You can see the right hand side is threaded and the left hand side is drilled and tapped. I was going to use my new M13x.8 tap/die but I didn't have a die holder that size. I will try the M13x.8 one next time.
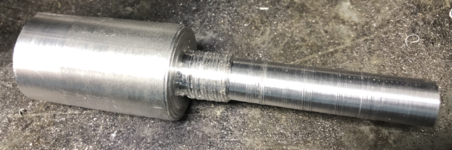
As you can see, the pen cap and the pen body screws on very nicely with the new mandrel and feels very secure/tight.
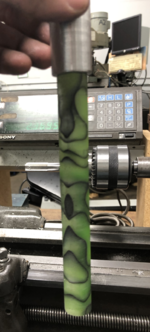
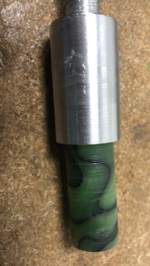
At first the pen cap and body screws and unscrews well but after a few times on and off the connection fails and the cap will slide off the body with almost no force.
What is strange to me is that if I thread the pen cap and pen body back on the mandrel, they are still very snug and tight on the mandrel. The same with the pen body, I can slide it on the mandrel and screw it onto the threads and it's on there tight.
I cutoff and resurfaced the body multiple times. My first attempt I used the die at 12.9mm thickness, that eventually failed. The 2nd attempt I started over and used the die at 13.1mm thickness and that failed in the same manner and the final attempt I cut it off/resurfaced and used the die at 14mm thickness and that failed as well.
Sorry, if I am missing something obvious. I am not sure why the pen parts connect snugly with the aluminum mandrel but not with each other.
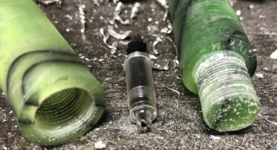
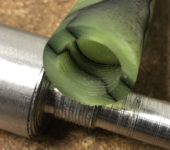
Any ideas/suggestions?
Thank you.
Regards,
Harry
I'm running into an issue joining a kitless pen cap and a pen body.
I made my own mandrel, as shown below. I plan to use it to hold the pen body and pen cap when I shape them on the lathe.
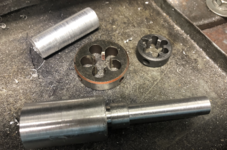
I used a M13x1 tap and die. You can see the right hand side is threaded and the left hand side is drilled and tapped. I was going to use my new M13x.8 tap/die but I didn't have a die holder that size. I will try the M13x.8 one next time.
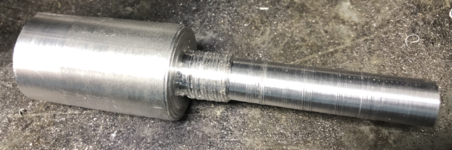
As you can see, the pen cap and the pen body screws on very nicely with the new mandrel and feels very secure/tight.
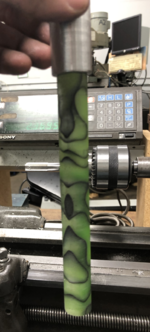
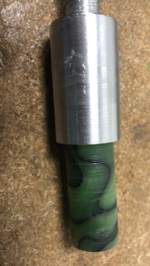
At first the pen cap and body screws and unscrews well but after a few times on and off the connection fails and the cap will slide off the body with almost no force.
What is strange to me is that if I thread the pen cap and pen body back on the mandrel, they are still very snug and tight on the mandrel. The same with the pen body, I can slide it on the mandrel and screw it onto the threads and it's on there tight.
I cutoff and resurfaced the body multiple times. My first attempt I used the die at 12.9mm thickness, that eventually failed. The 2nd attempt I started over and used the die at 13.1mm thickness and that failed in the same manner and the final attempt I cut it off/resurfaced and used the die at 14mm thickness and that failed as well.
Sorry, if I am missing something obvious. I am not sure why the pen parts connect snugly with the aluminum mandrel but not with each other.
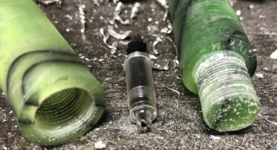
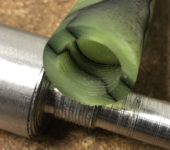
Any ideas/suggestions?
Thank you.
Regards,
Harry
Last edited: