egnald
Member
Greetings from Nebraska.
Today I made a new set of Sleeves for my PSI Pen Assembly/Disassembly Press. The ones I have been using were starting to get marred up pretty bad and I hadn't made them long enough that I could just re-face them - an oversight that I corrected on the new set. I turned them from white 1-1/2" inch UHMW rod. The hole in the long one, which slips over the spring loaded factory plastic piece, was drilled out with a 30mm forstner bit. The hole in the short one, which slips over the aluminum piece, was drilled out with a 1" forstner bit.
I like them much better than pressing my parts between the factory one that has a tapered hole in it and the hard aluminum piece. I think that the UHMW gives me just a little more cushion between the kit parts when I am pressing them in. I also had problems in the past with the tapered hole occasionally causing marks on the nib/tips of my kits.
For me, making jigs or jig parts like this can be just as satisfying as making pens.
Regards.
Dave
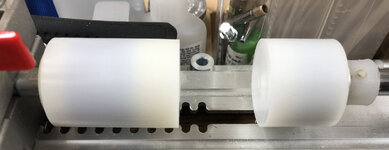
PS Although I didn't snap a picture of it, I also made one of the short one's with a 31/64" inch recess hole drilled in its face. This hole accommodates the rounded top on the cap/clip of the Sierra style kits and holds it square during pressing. It makes it much easier by not having to try to hold the part straight when its rounded end is against a flat press surface. It's not my own idea, it was something that learned from Ed in one of his Exotic Blank video shorts.
If you are not familiar with the Exotics' Short Vids, I highly recommend you check them out. Ed's slightly older videos can be found on the "Ed from ExoticBlanks" YouTube channel.
Today I made a new set of Sleeves for my PSI Pen Assembly/Disassembly Press. The ones I have been using were starting to get marred up pretty bad and I hadn't made them long enough that I could just re-face them - an oversight that I corrected on the new set. I turned them from white 1-1/2" inch UHMW rod. The hole in the long one, which slips over the spring loaded factory plastic piece, was drilled out with a 30mm forstner bit. The hole in the short one, which slips over the aluminum piece, was drilled out with a 1" forstner bit.
I like them much better than pressing my parts between the factory one that has a tapered hole in it and the hard aluminum piece. I think that the UHMW gives me just a little more cushion between the kit parts when I am pressing them in. I also had problems in the past with the tapered hole occasionally causing marks on the nib/tips of my kits.
For me, making jigs or jig parts like this can be just as satisfying as making pens.
Regards.
Dave
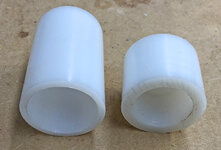
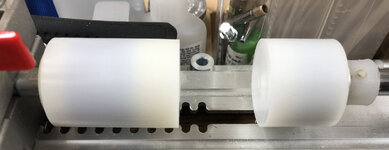
PS Although I didn't snap a picture of it, I also made one of the short one's with a 31/64" inch recess hole drilled in its face. This hole accommodates the rounded top on the cap/clip of the Sierra style kits and holds it square during pressing. It makes it much easier by not having to try to hold the part straight when its rounded end is against a flat press surface. It's not my own idea, it was something that learned from Ed in one of his Exotic Blank video shorts.
If you are not familiar with the Exotics' Short Vids, I highly recommend you check them out. Ed's slightly older videos can be found on the "Ed from ExoticBlanks" YouTube channel.