mark james
IAP Collection, Curator
A bit of a more classy pen for me (actually, is a gift for another pen maker/artist).
Comments and critique are welcomed.
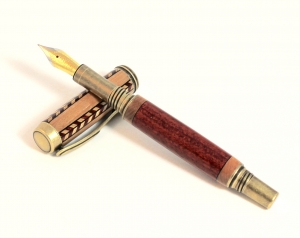
View in Gallery
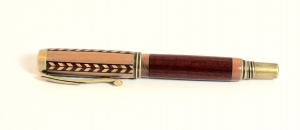
View in Gallery
Comments and critique are welcomed.
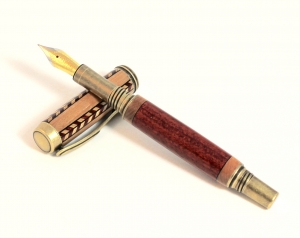
View in Gallery
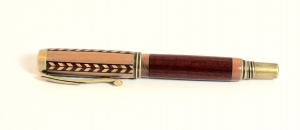
View in Gallery