I found this subject is somehow hidden or not widely explained due to trade secrets or who knows why )))
Here is example of blanks, that i am talking about. The main idea, that used in public videos - is to cast thin sheet of epoxy resin, then put it inside the form, pour in another resin - and voila - blank is ready. But when i am trying to reproduce such scenario i found:
1. The ribbons on pics much thinner, that mine - it is look like their thickness is about 0.3-0.5 mm
2. During the exoterm peak - my ribbon becames soft, and the folds have tendency to straightens out.
3. Also the look of ribbons in pics are more like fabric folds, look very natural and random.
4. In such bunch of folds - how the bubble problem need to be solved?
So i think the ribbons material could be not only self made sheets, but also ... PVC sheets or maybe another plastic sheets?
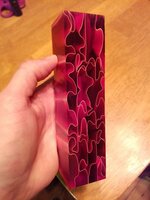
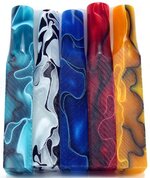
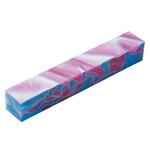
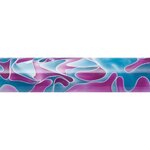
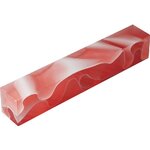
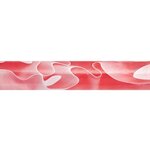
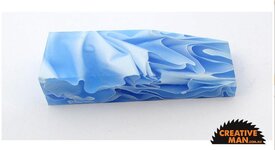
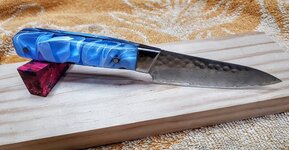
Here is example of blanks, that i am talking about. The main idea, that used in public videos - is to cast thin sheet of epoxy resin, then put it inside the form, pour in another resin - and voila - blank is ready. But when i am trying to reproduce such scenario i found:
1. The ribbons on pics much thinner, that mine - it is look like their thickness is about 0.3-0.5 mm
2. During the exoterm peak - my ribbon becames soft, and the folds have tendency to straightens out.
3. Also the look of ribbons in pics are more like fabric folds, look very natural and random.
4. In such bunch of folds - how the bubble problem need to be solved?
So i think the ribbons material could be not only self made sheets, but also ... PVC sheets or maybe another plastic sheets?
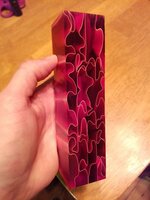
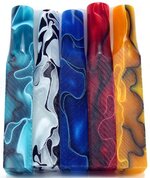
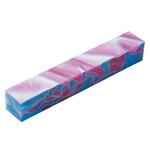
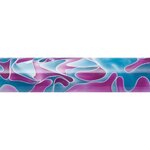
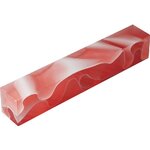
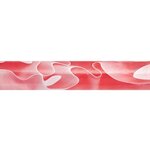
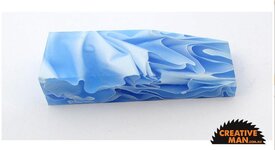
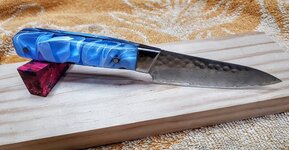