DurocShark
Member
I've got a bunch of old hawaiian print shirts that are in various states of disrepair. In the back of my head I've been thinking that I could pen-itize them. I didn't want to sleeve a tube though.
I soaked some cut up strips in weakly catalyzed PR (3 drops per ounce... Enough to get it to gel up) and stuffed them in a pipe mold. They cured in the toaster oven for a few hours and came out looking really good.
So I drilled a piece and started to turn it. The material made the blank weak and it snapped at a piece of cloth. I know there are voids... The joys of trying something like this without pressure. I had figured on filling them with thick CA or something.
Anyway, I have a question... Anybody else tried something like this? I can wrap and cast tubes all day long, but this seems different. Would pressure harden the PR in the cloth fibers where just soaking and wringing the material didn't?
Obligatory pic:
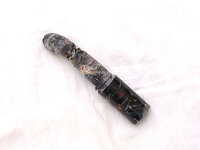
I soaked some cut up strips in weakly catalyzed PR (3 drops per ounce... Enough to get it to gel up) and stuffed them in a pipe mold. They cured in the toaster oven for a few hours and came out looking really good.
So I drilled a piece and started to turn it. The material made the blank weak and it snapped at a piece of cloth. I know there are voids... The joys of trying something like this without pressure. I had figured on filling them with thick CA or something.
Anyway, I have a question... Anybody else tried something like this? I can wrap and cast tubes all day long, but this seems different. Would pressure harden the PR in the cloth fibers where just soaking and wringing the material didn't?
Obligatory pic:
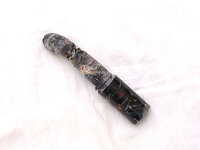