jttheclockman
Member
Remember these pens???
Well people have asked how I make them. Unfortunately I did not take alot of photos but will post some and you can get the basic idea and the tools I used to do these and the others that I used the dots on. When I do more like these I will take more photos. I will try to take more photos of any new design I come up with. Any questions I will be happy to address here.
I made a platform for my trim router that allows me to cut slots, drill holes, and other functions which I intend to show at a later date. My shop time is still nonexistant for a couple more weeks. Along with this jig I used my indexing wheel which is an add-on. I will show this in a photo also.
I will show the parts to make the black and white one and the red one was done the same way. As I said I do not have a metal lathe so I use whatever woodworking tools I have and you will be surprised at what you can do.
There are other ways of doing what I do as well as other jigs that can be made and hopefully others will show some of theirs too. But for now lets get things started as requested by Skiprat and others. Here is some photos.
Don't mind the blanks on the right. They were for another pen. The ones of interest are the strpe ones.
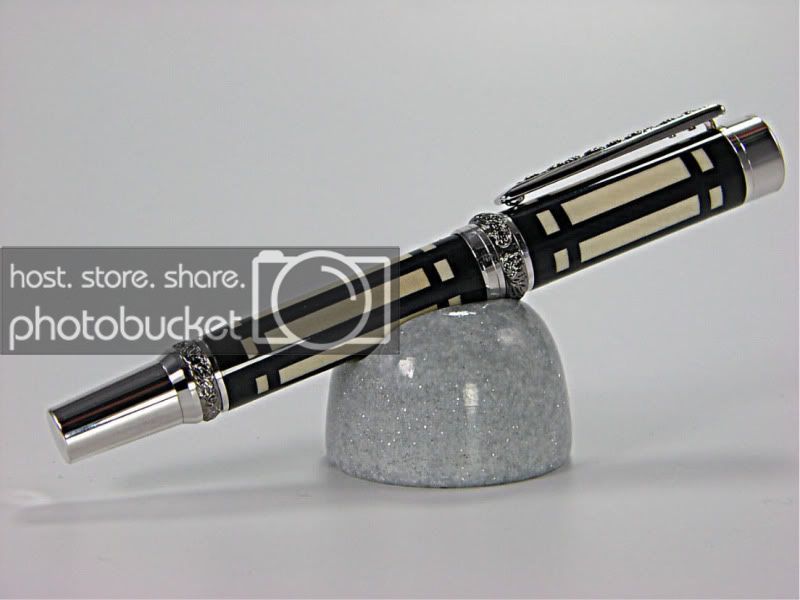
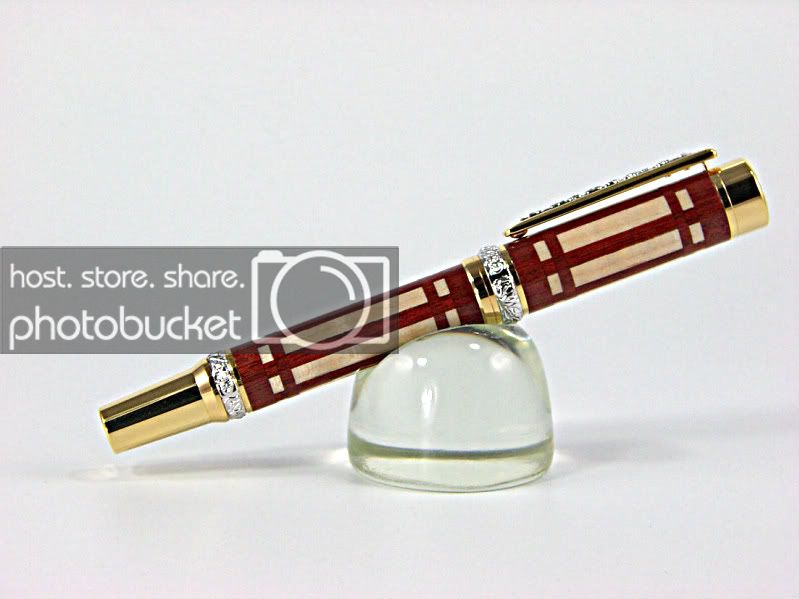
Well people have asked how I make them. Unfortunately I did not take alot of photos but will post some and you can get the basic idea and the tools I used to do these and the others that I used the dots on. When I do more like these I will take more photos. I will try to take more photos of any new design I come up with. Any questions I will be happy to address here.
I made a platform for my trim router that allows me to cut slots, drill holes, and other functions which I intend to show at a later date. My shop time is still nonexistant for a couple more weeks. Along with this jig I used my indexing wheel which is an add-on. I will show this in a photo also.
I will show the parts to make the black and white one and the red one was done the same way. As I said I do not have a metal lathe so I use whatever woodworking tools I have and you will be surprised at what you can do.
There are other ways of doing what I do as well as other jigs that can be made and hopefully others will show some of theirs too. But for now lets get things started as requested by Skiprat and others. Here is some photos.
Don't mind the blanks on the right. They were for another pen. The ones of interest are the strpe ones.
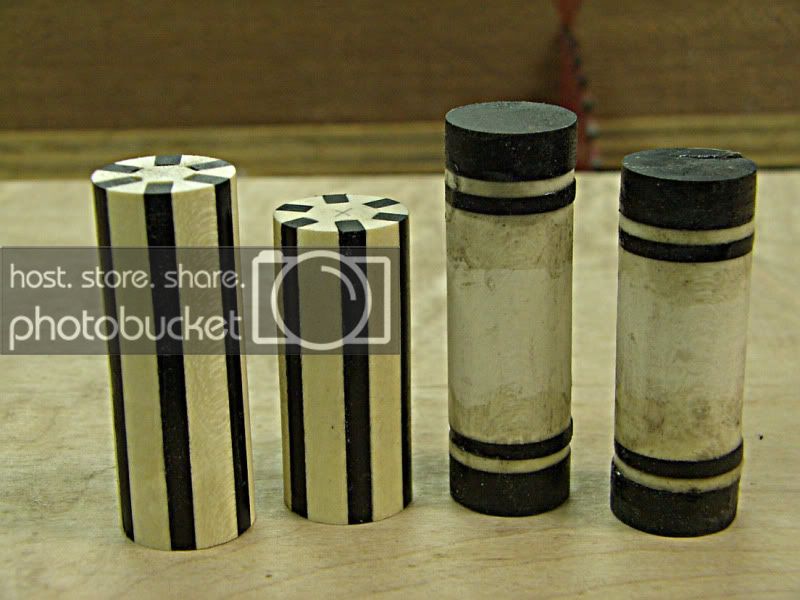
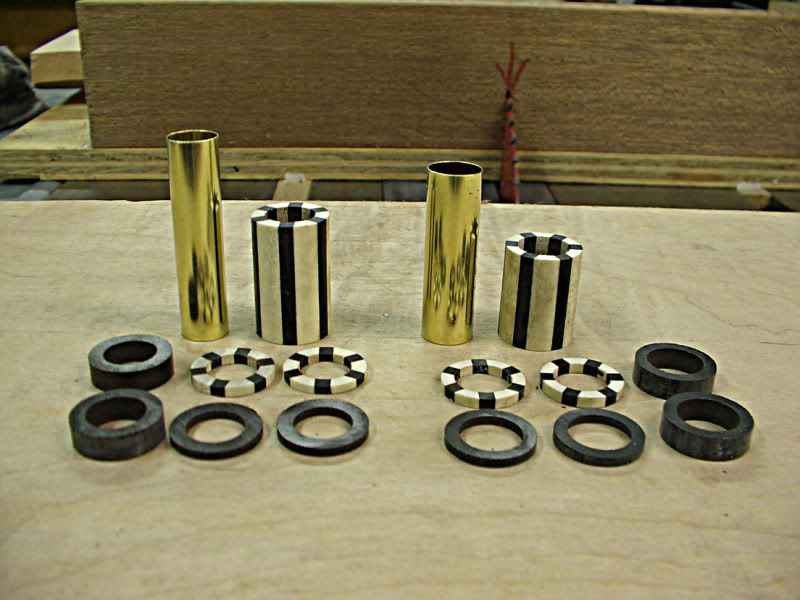
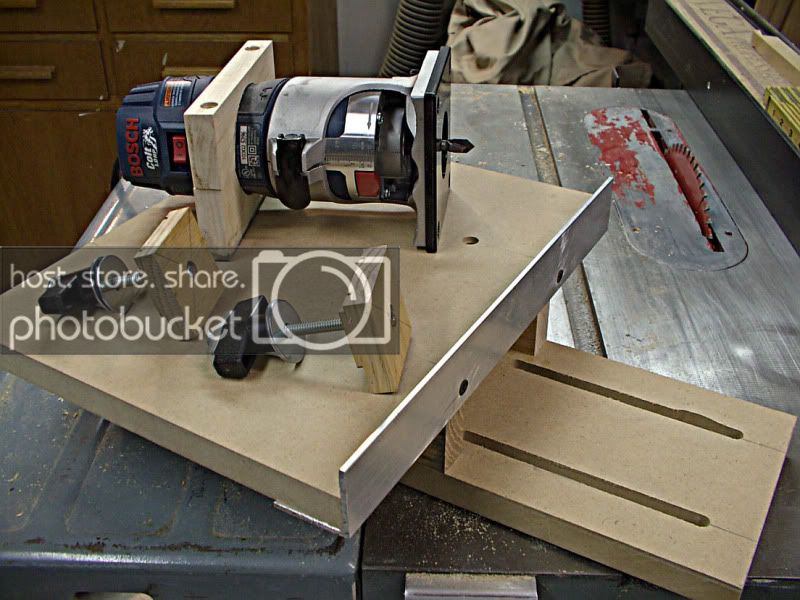
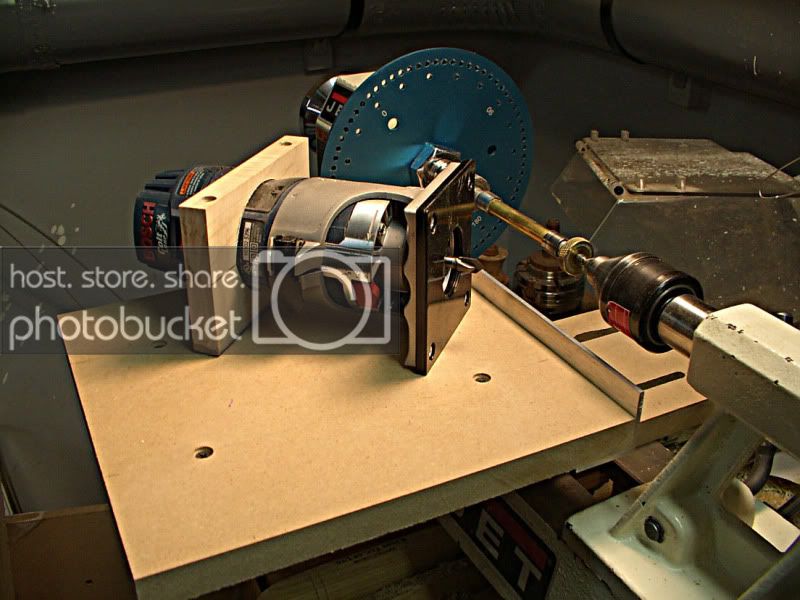