PTownSubbie
Member
Some questions have been floating around here on using PVC as a mold for PR and other casting products. I could not get the PR to come out of the PVC very well so I looked for other options. The one I came up with was to make my own round verticle molds.
I made my molds using OOMOO 25 & OOMOO 30 silicone. The OOMOO 25 seems to work better for our application IMO. It is a little more forgiving when you pull on it than the 30 is. I can by my silicone locally from a small company so I don't have to get it online. If you can't find it locally, you can find it here: http://www.smooth-on.com/OOMOO=-Silicone-/c1136/index.html?catdepth=1 This is not the only thing out there and I have no affiliation but am just a fairly satisfied user.
You start with a 1/2" and 1-1/2" PVC pipes. I cut the 1-1/2" PVC pipes on my tablesaw by holding the top with a clamp so that my hands are far from the blade as possible. BE CAREFUL when you do this. The round PVC may try to rotate on you and bind with the blade. This is true any time you cut round things. There are other ways to cut this but such as a bandsaw or even a hand saw. The straightness of the cut is not ultra important here.
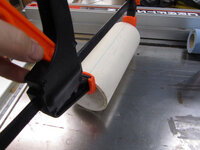
Next turn down a small piece of wood and insert it into one end of the 1/2" PVC pipe and glue it in place. This will be used to screw down on the bottom piece. Center this 1/2" PVC pipe on the bottom of the mold and put a screw through it as shown. (The outer pipe is not cut in half just for show, it has to be cut into two pieces or you will never get the silicone mold out of it. Just tape it together before you pour your silicone and it will hold just fine.)
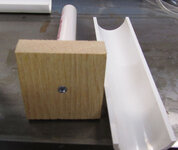
Next plug the other end of the 1/2" PVC pipe with anything of your choice. I used some Clay I had lying around. As you can see, the inner pipe is slightly shorter than the outer 1-1/2" PVC pipe. This is so you can cast completely overtop of the inner pipe and get a solid bottom.
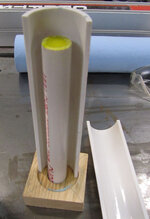
The finished molds are show here. The most difficult part of working with these molds comes when trying to remove the finished cast. You have to work it out slowly like an inch worm. That is the best way I can describe it.
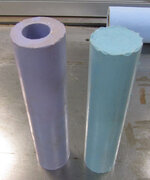
It might not be the best solution around but you don't have to mess around with PVC and beating the casts to get them out. That beating has to cause some hairline cracks in the cast to some level. No beating here.
If anyone has any questions, ask away or PM me. I know there are ways to improve on this but I don't know how many people would be interested in something like this...
I made my molds using OOMOO 25 & OOMOO 30 silicone. The OOMOO 25 seems to work better for our application IMO. It is a little more forgiving when you pull on it than the 30 is. I can by my silicone locally from a small company so I don't have to get it online. If you can't find it locally, you can find it here: http://www.smooth-on.com/OOMOO=-Silicone-/c1136/index.html?catdepth=1 This is not the only thing out there and I have no affiliation but am just a fairly satisfied user.
You start with a 1/2" and 1-1/2" PVC pipes. I cut the 1-1/2" PVC pipes on my tablesaw by holding the top with a clamp so that my hands are far from the blade as possible. BE CAREFUL when you do this. The round PVC may try to rotate on you and bind with the blade. This is true any time you cut round things. There are other ways to cut this but such as a bandsaw or even a hand saw. The straightness of the cut is not ultra important here.
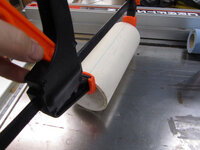
Next turn down a small piece of wood and insert it into one end of the 1/2" PVC pipe and glue it in place. This will be used to screw down on the bottom piece. Center this 1/2" PVC pipe on the bottom of the mold and put a screw through it as shown. (The outer pipe is not cut in half just for show, it has to be cut into two pieces or you will never get the silicone mold out of it. Just tape it together before you pour your silicone and it will hold just fine.)
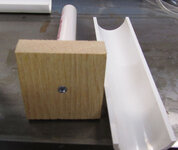
Next plug the other end of the 1/2" PVC pipe with anything of your choice. I used some Clay I had lying around. As you can see, the inner pipe is slightly shorter than the outer 1-1/2" PVC pipe. This is so you can cast completely overtop of the inner pipe and get a solid bottom.
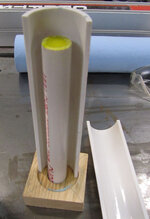
The finished molds are show here. The most difficult part of working with these molds comes when trying to remove the finished cast. You have to work it out slowly like an inch worm. That is the best way I can describe it.
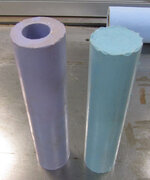
It might not be the best solution around but you don't have to mess around with PVC and beating the casts to get them out. That beating has to cause some hairline cracks in the cast to some level. No beating here.
If anyone has any questions, ask away or PM me. I know there are ways to improve on this but I don't know how many people would be interested in something like this...